Consider the environmental impacts of oil loss by implementing a Preventative Maintenance programme for your hydraulic machinery.
Learn the benefits of preventive maintenance and see the signs to look for when to change the hydraulic hoses. Heavy Machines are kept in top working order through preventative maintenance to avoid oil leakage and loss and prevent contamination of the ground and surface water.
Benefits of Preventative Maintenance and Checklist
There is nothing worse than having a hydraulic hose blow, oil spraying everywhere, at that crucial moment in the working day, setting you back hours or sometimes days.
For civil and forestry businesses, unplanned downtime drives up the costs of a project and severely hinders productivity. Whilst we all know this can happen, it is hard to predict, and keeping on top of your machines with preventive measures is the best way to combat the unplanned.
The preventative maintenance process involves assessing the state of the hydraulic hose and understanding when it’s time to replace it before the hose blows unexpectedly in operation. This unexpected blow, can not only affect your project delivery times and profitability but also the machine's performance and the amount of oil lost or spilt.
Reports back from our customers have advised that prior to preventative maintenance they were losing on average, around 40-60 litres of oil per hose failure. At approximately $3-6 per litre this was not only a hit to their bottom line but also left an impact on the environment they were working in. Machines kept in top working order through preventative maintenance avoid oil leakage and loss and prevent contamination of the ground and surface water. A BOA customer recently commented that “by performing proactive maintenance we can pick up worn hoses and are able to change them before they blow”.
The benefits of preventive maintenance are;
- We don’t have downtime on site.
- We aren’t pouring oil into the ground.
- We’re not holding up the crew or a truck up because you can get it sorted before it blows to pieces.
Many of our other BOA customers also report back that they have made significant savings across all their machines, by working on a preventative maintenance programme.
There are a number of key signs and checklists to look for at the time of maintenance to signal a hose replacement is required:
- Inspect for external cuts or abrasions - look for ones greater than a normal scratch.
- Twisted or crushed hoses can lead to a dangerous build-up of pressure and should be replaced immediately.
- Monitor the number of hours your hoses have done. Log this information against each of your assets, allowing you to know when to replace hoses, after a designated number of hours.
- Oil leaking along the hose is a clear indication that the hose should be replaced.
- Worn spots or cracks on the hose are a clear signal that the hose needs to be replaced and that area of the new hose should be monitored for wear and tear.
- Leaks or cracks around the fittings indicate an issue with the hose & fitting assemble and should be rectified immediately.
All of the above, if not addressed during preventative maintenance, can lead to a blown hydraulic hose or create issues for other parts of the machine that can be even more costly.
What better way to get the most out of your valuable machine investment, than to get into the good habit of preventative hydraulic hose maintenance? With a programme in place and a log of the maintenance performed, you can avoid hose failure, expensive machine repairs, adverse environmental impacts and costly downtime.
By planning for the unplanned, companies can turn wasted time back into profit and keep their costs down and the environment protected.
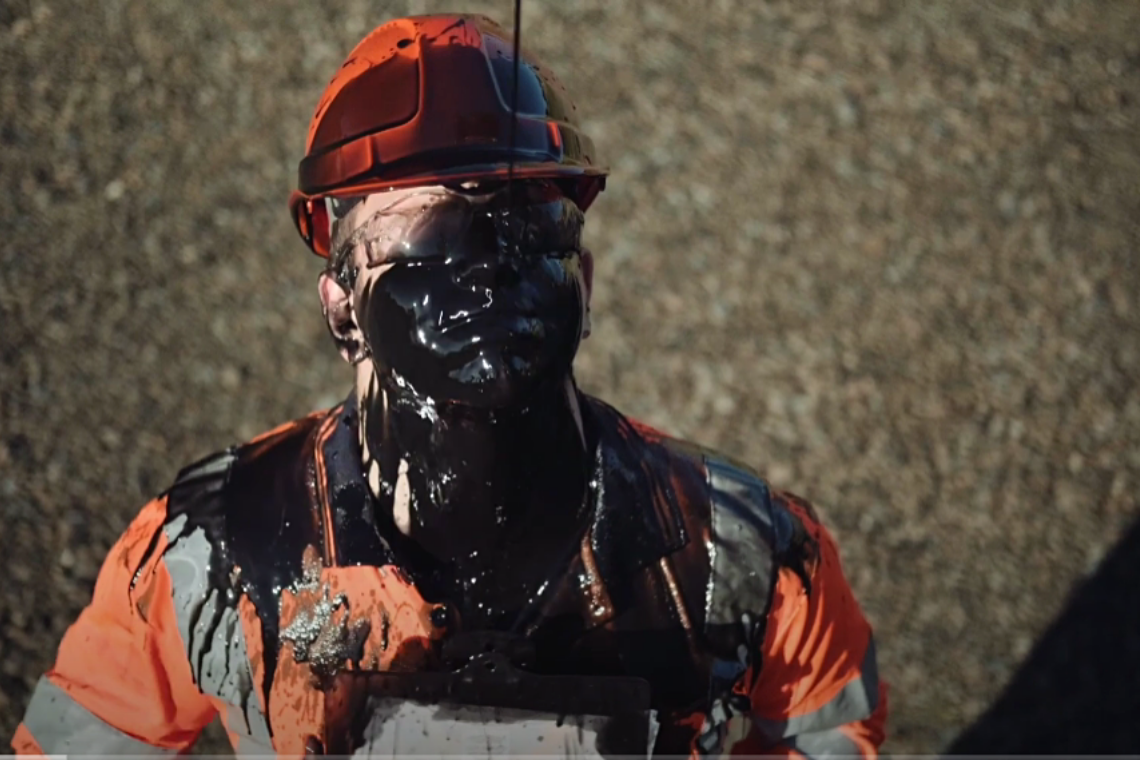