Planning the unplanned: How does preventative hydraulic hose maintenance reduce downtime?
Planning the unplanned: How does preventative hydraulic hose maintenance reduce downtime? Learn why and how a proactive approach to hydraulic hose maintenance can significantly reduce downtime on heavy machinery.
Currently, most hydraulic machinery owners and operators take a reactive approach to fixing damaged hydraulic hoses; when a hydraulic hose blows onsite, crew members are forced to stop operating and wait for a hose technician to replace it. The time it takes to get back up and running varies, and the costs associated with callout and replacement fees – not to mention oil lost from the blown hose – can add up for contractors.
Contractors can reduce unplanned downtime by scheduling preventative hydraulic hose maintenance. This way, downtime is predictable, controllable, and doesn’t interfere with operations. Furthermore, hydraulic asset owners can make significant savings in terms of time, money, and oil loss from unplanned hydraulic hose failure.
Traditional hydraulic hose repair model is reactive
The current attitude towards hydraulic hose repair and maintenance is reactive. Contractors will often wait until a hose has blown and operations have stalled to seek out a hose technician.
This approach means that contractors expose themselves to several unknown variables outside of their control, including:
- Callout and service fees of the closest hydraulic hose technician
- The amount of downtime the crew experiences while on the job
- The amount of oil lost onsite due to unexpected hydraulic hose failure.
Without knowing the values of the above, hydraulic machinery owners and operators can’t easily work productively or plan their time and budgets with certainty.
The proactive approach to hydraulic hose maintenance addresses these variables, giving contractors greater control, greater certainty over how they will spend their time, and greater profitability on their hydraulic machinery. This is known as Hydraulic Uptime.
Just as we schedule maintenance and servicing for our cars to avoid any breakdowns when we need our vehicles the most, companies should practice proactive scheduling for hydraulic hose maintenance.
By developing a proactive attitude toward hydraulic assets, companies can reduce their downtime by up to 85% - saving time, money, and oil, and getting greater use out of their machines.
Why do preventative hydraulic hose maintenance?
Planned maintenance of hydraulic machinery is preventative. This is because it has a direct correlation to that machine’s productivity, and therefore, its profitability. There are several benefits to thinking ahead, including:
- Avoiding unexpected hose failure and eliminating unplanned downtime on the job
- Saving money from urgent callout fees for hose technicians
- Reducing the amount of oil lost onsite for a lower environmental impact.
Preventative hydraulic hose maintenance enables machines to perform at their best when it matters the most (during work hours). A large number of hydraulic machinery owners run scheduled maintenance programs, where heavy machinery is scheduled for a full service before it breaks down in the field. This process includes replacing damaged tracks, dirty oil, and leaky rams, but not hydraulic hoses. Shifting away from reactive hydraulic hose repair allows companies to turn wasted time back into profit.
The hydraulic machinery industry is moving forward. Companies who are not thinking proactively about their assets and optimizing their savings will soon struggle to compete with those in their industry who are.
Calculate your potential savings with BOA Hydraulics
The first step to reducing downtime is understanding the current costs of a company’s hydraulic hose and repair activities.
The BOA Uptime Calculator provides a full picture of how much companies are spending on hydraulic hose repairs currently.
Using information about a company’s industry and the number of hydraulic assets in operation, the Uptime Calculator illustrates how much hydraulic machinery owners are spending on:
- Hydraulic downtime while on the job
- Repair and replacement of hoses and fittings
- Oil lost onsite due to hydraulic hose failure.
With this information, the Uptime Calculator then calculates a company’ potential savings through proactive hydraulic hose repair and maintenance.
BOA’s solution for greater productivity and profitability
When scheduled hydraulic maintenance becomes the norm, companies eliminate unexpected hydraulic downtime, saving time, money and oil.
BOA Hydraulics offers an integrated solution that enables hydraulic machinery owners to transition towards proactive and preventative maintenance. This solution includes:
- The BOApod: a mobile, all-terrain facility for the assembly of hydraulic hoses in the field
- Comprehensive hydraulic hose repair training and support for the safe assembly and replacement of hydraulic hoses by crew members
- The BOAhub: A hydraulic hose management system. This is a multi-device app for accurate hose building, planned maintenance, reducing unplanned hose failure, reducing oil loss, inventory management, and reporting
- Top quality hoses and fittings products from trusted global brands, including Yokohama, Uniflex, and DNP for longer hose lifespan in higher pressure environments.
With the right technology, training, and tools, BOA empowers businesses to take back control of their hydraulic assets. Asset owners therefore, have greater autonomy, with the power to improve the productivity and profitability of their hydraulic machines.
We'll support your hydraulic hose preventative maintenance programme
It’s never too late to rethink and restart your hydraulic hose repair and maintenance programme. Contact the team at BOA Hydraulics to transition towards preventative hydraulic hose maintenance for greater savings, success, and Hydraulic Uptime.
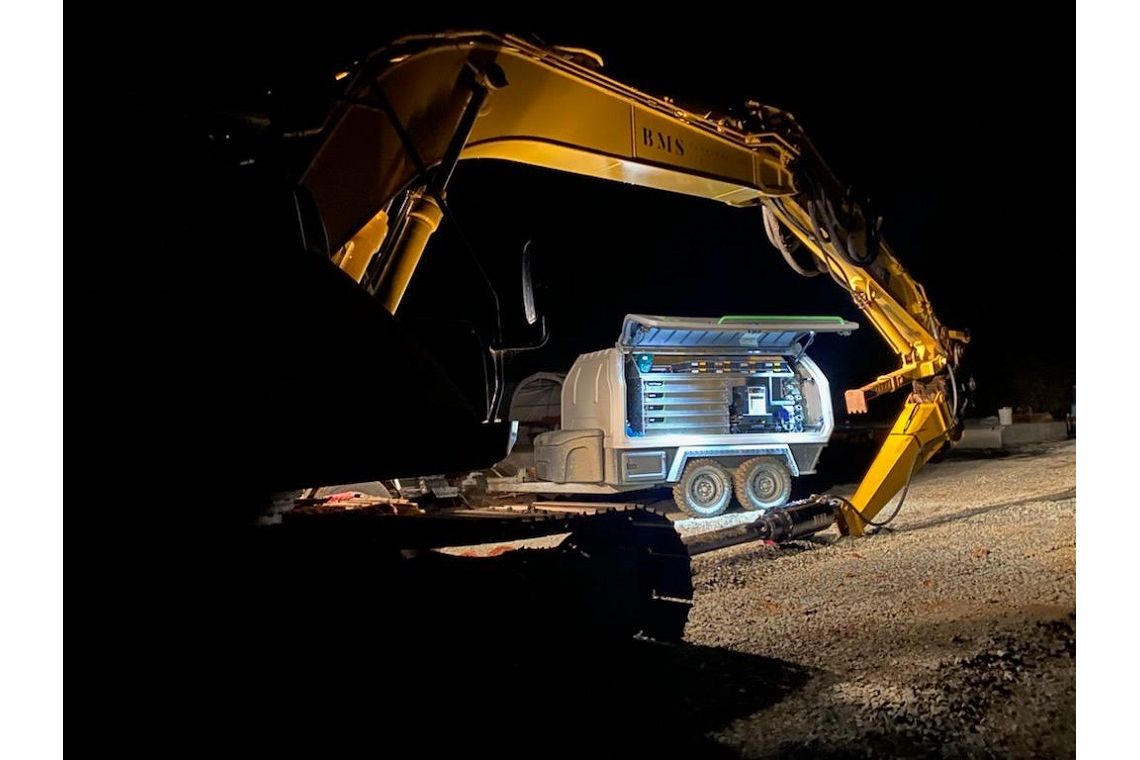