5 Major Industries That Rely on Hydraulic Machinery in New Zealand
Many of New Zealand’s primary industries rely on hydraulic machinery to support smooth operations. Forestry, mining, civil, demolition, and quarrying operations face similar challenges when it comes to avoiding downtime for uninterrupted operations.
Learn some of the shared challenges these hydraulic machine operators face, and how hydraulic hose management can reduce downtime on the job.
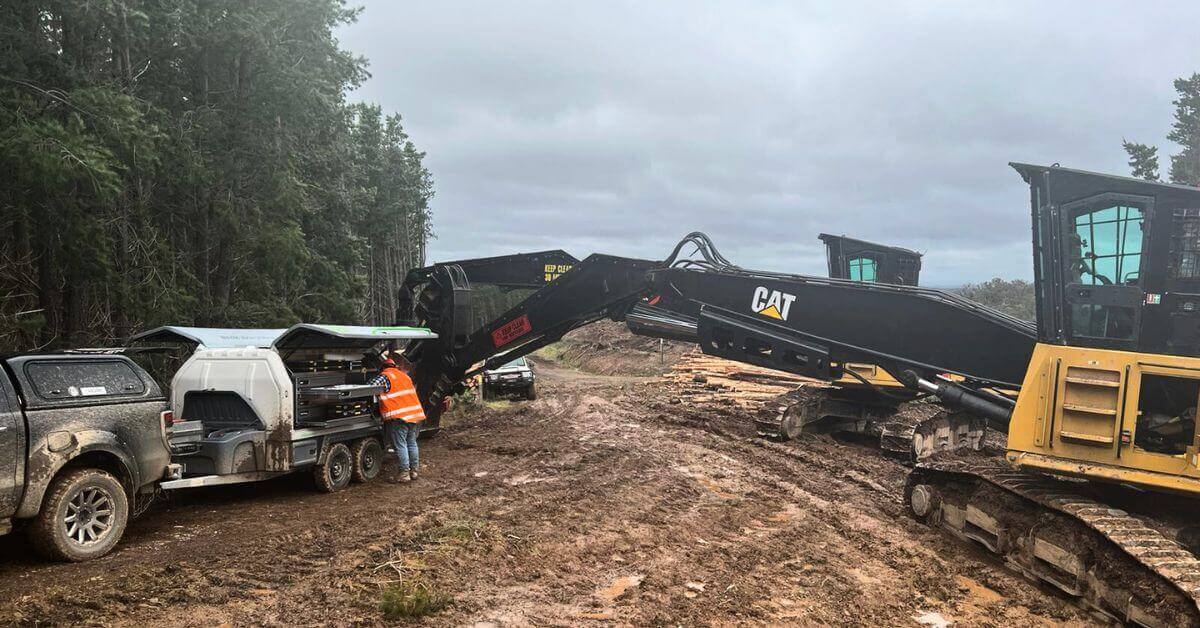
1. Forestry
According to Ministry for Primary Industries (MPI), forests contribute $6 billion each year to our economy.
The forestry industry relies heavily on hydraulic systems and components to operate efficiently. Forest terrain is rough and demands a lot from machinery – normally resulting in significant wear and tear on hydraulic hoses.
Delimbers, feller bunchers, mulchers, yarders, forwarders, loaders, and harvesters all depend on hydraulic hoses to operate.
As forestry contractors are mostly paid by the amount of wood they can move, it’s crucial to keep these machines working.
Any hydraulic hose failure results in machine and staff downtime that stalls operations and increases the overall costs of the project. In remote locations, hose technicians are far from the site which can mean steep callout fees and longer wait times. When a hose blows unexpectedly, machines can lose a significant amount of hydraulic oil, negatively impacting the environment.
Forestry contractors can’t afford to have their machines and crew on the sidelines during operational hours waiting for a fix. Nor is it appropriate to leave regular, harmful oil spillages on the forest floor.
Thankfully, operators can attend to blown hoses quickly and efficiently, getting machines back online in 30 minutes or less. Furthermore, replacing worn hoses prevents hydraulic failure, reduces unplanned downtime during crucial operational hours, and minimizes harmful environmental impacts.
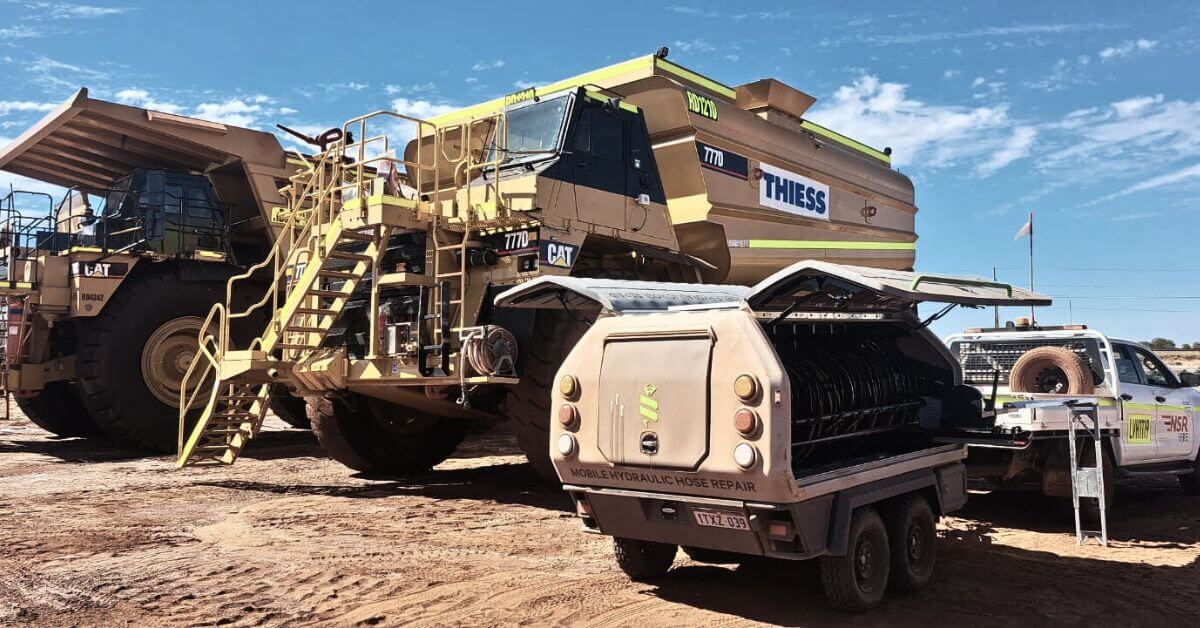
2. Mining
Mining is another key industry in New Zealand that depends on hydraulic machinery for smooth operations. Miners use a wide range of machinery to excavate and move valuable minerals and ores.
Like the forestry industry, mines are typically remote locations, and hydraulic machines operate in rough terrain with high-pressure tasks. Earth movers, crushing equipment, excavators, transporters, drills, and feeding equipment all rely on hydraulic power to drive them.
Every minute that precious material isn’t being retrieved and transported is money lost for mines. New Zealand’s gold mines, for example, can’t earn income from gold stuck onsite due to hydraulic machinery being down.
Downtime is therefore a crippling issue for mining projects and accumulates steep additional costs for operators. According to the University of Wollongong Australia, 37% of machine downtime in the mining industry is due to hydraulic hose failure.
Implementing a full hydraulic hose repair and maintenance programme for hydraulic mining equipment can therefore reduce costs of operations. Deliberate hydraulic hose maintenance keeps machines and people engaged during operational hours, boosting productivity and profitability of the project.

3. Civil Construction
A range of hydraulic machinery is involved in civil construction projects.
Construction engineering and management, transport and structural engineering projects require the movement of earth and heavy materials to carry out:
- Earthwork projects
- Roadway, bridge, railroad and airport construction
- Canals and river stabilization or widening
- Wastewater treatment activities
- Dams and reservoir establishment.
Civil construction projects are typically located in more populated areas, giving them easy access to local hose technicians. Civil construction budgets typically factor in hydraulic hose failure, especially when submitting a bid for large contracts.
So, if hydraulic hose repair is budgeted for, and hose technicians are readily available, how could civil contractors improve productivity of their hydraulic assets?
Civil contractors should consider the benefits of carrying out preventative maintenance on hydraulic machinery that includes repairing and replacing hoses.
Currently, when civil contractors schedule a machine for maintenance, this service may include an assessment of rams, tracks, cabs and engine. The scheduled maintenance frequently excludes servicing hydraulic hoses.
In addition to the scheduled maintenance downtime, hydraulics assets will therefore experience further unplanned downtime when a worn hose finally fails. This is costly for civil projects, especially when front-line machines experience stoppages, as this also halts work for several other machines – and teams. Fortunately, it is preventable.
Scheduling preventative maintenance that includes repairing and replacing hoses on machinery limits the risk of further downtime delaying operations.
4. Demolition
Demolition projects are notorious for their heavy-duty machinery requirements, and the impact these operations have on hydraulic hoses.
Excavators, material handlers, scrap shears, hydraulic hammers, and pulverizes all depend on quality hoses for smooth operations.
Abrasions, cuts, poor hose routing, heat aging, and fitting failures lead to a high rate of hose failure in demolition. When moving materials, there’s a high chance of hydraulic hoses getting caught on protruding surfaces and cut on metal edges. This results in frequent hose fatigue and failure in demolition equipment.
This becomes costly for demolition contractors. Regular hose failure means regular downtime for staff and crews, which heavily impacts productivity and the overall profitability of the project.
Demolition operators should therefore consider an onsite solution for safe hydraulic hose assembly and replacement to reduce this downtime. Not only can staff learn to safely replace these hoses immediately, but also to carry out preventative hose maintenance to avoid unplanned downtime altogether.
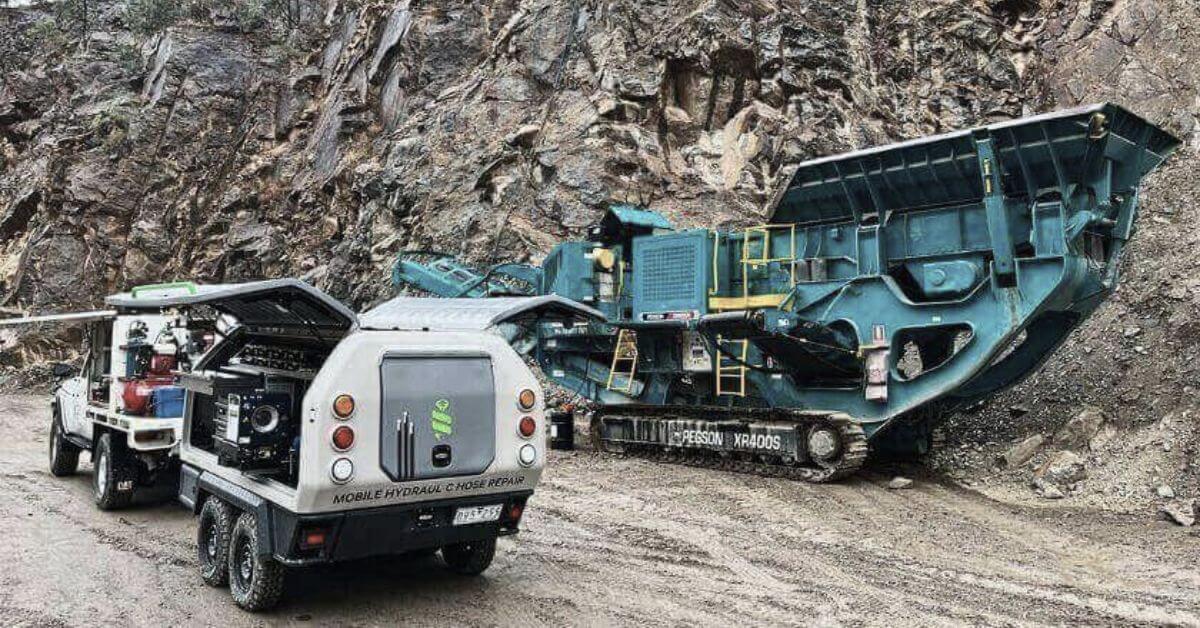
5. Quarrying
Like mining, quarrying relies heavily on hydraulic-run machinery to extract, crush/process, and deliver the material.
Similarly, quarry locations are dependent on the land’s geological makeup, meaning some sites can be isolated from local townships.
Quarrying operations require thoughtful planning, and hydraulic hose management should be part of this process. Quarriers experience significant downtime issues when a hydraulic hose on a front-line machine blows; if operators can’t extract rock from the quarry, the rest of the operation stalls until those machines are back online. On top of that staff and machine downtime, hose repair callouts can be expensive, especially if the site is far from the nearest technician.
Quarry operators should therefore seek a solution that allows quarry operators to turn that wasted time back into profit. Staff onsite should assess hydraulic hoses for signs of damage and bring a mobile hose repair and maintenance solution onsite to reduce downtime.
Reducing downtime on hydraulic machinery
The BOA Integrated Solution reduces downtime for operators in forestry, mining, civil, demolition, quarrying, and other industries in New Zealand.
With innovative products, quality tools, and comprehensive training and ongoing support, we empower contractors to:
- Assemble and replace hydraulic hoses onsite
- Get their machines back up and running in under 30 minutes
- Carry out preventative maintenance to avoid unplanned downtime
- Reduce their hose bills by 40-60%.
Heavy machinery owners and operators can take back control of their machine downtime by planning ahead and servicing their hoses before stoppage occurs. Talk to the friendly team at BOA Hydraulics about how we can support you to increase productivity and profitability on your hydraulic machinery. Call us on 0800 20 20 20 or contact us through our website.
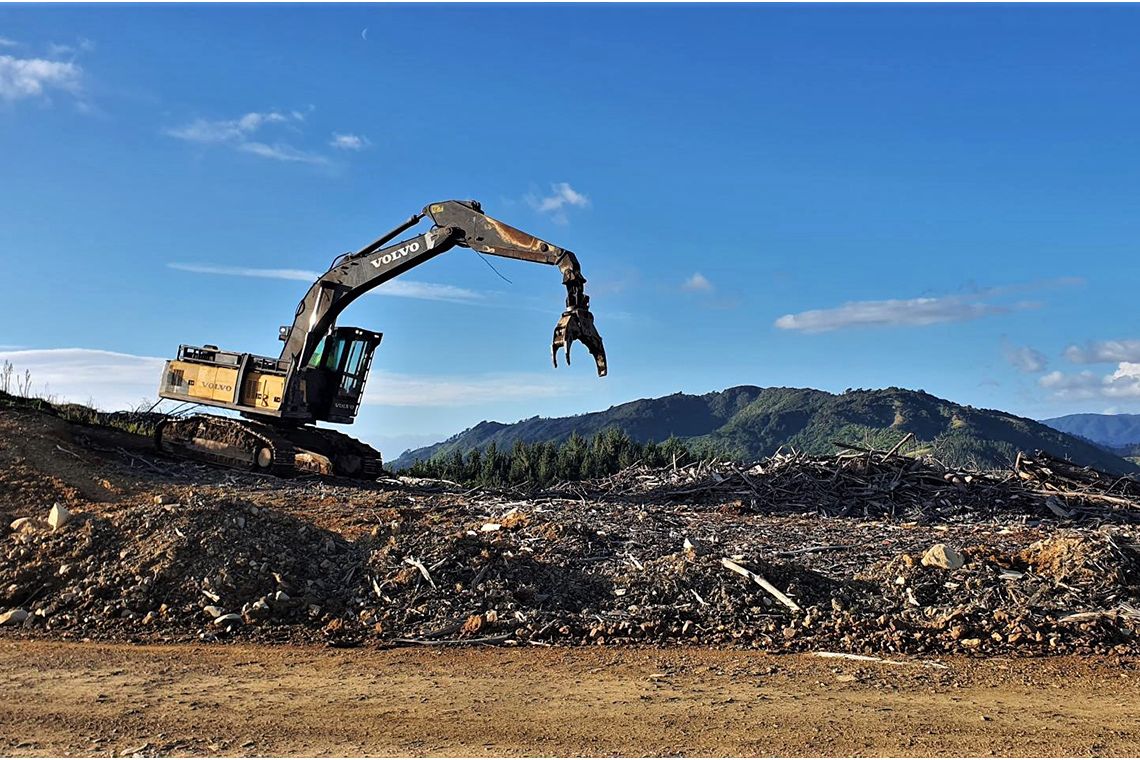