Hydraulic Maintenance for Heavy Machinery
Our Hydraulic Maintenance is for Heavy Machinery. The onsite hydraulic maintenance and repair programme is called the BOA Integrated Solutio. With this model, you’ll have all the right tools, training, and technology at your disposal to manage your own mobile hydraulic hose repair and replacement, and reduce downtime on the job.
Hydraulic Maintenance for Heavy Machinery
Find out how contractors in New Zealand’s primary industries are making significant savings and increasing their Hydraulic Uptime with the BOA Integrated Solution.
How does the BOA Integrated Solution work?
There are four key components to the BOA Integrated Solution that enable companies to achieve Hydraulic Uptime:
1. The BOApod: mobile hydraulic hose repair
The BOApod is a state-of-the-art hydraulic hose facility for mobile hydraulic hose repair and -assembly in the field.
With the BOApod, heavy machinery operators have access to:
- German-made Uniflex cutoff saw and crimper
- Vice for removing adaptors from hose fittings
- Air compressor for removing debris from new hoses
- Remote-controlled hose reel system to avoid heavy lifting
- Hose support stand for measuring, and keeping new hoses off the ground
- Onsite office space with charging ports for invoicing and other administrative tasks
- Aluminum fitting cabinet with workbench and storage for 200 different types of fittings
- Charging ports or solar panel for charging batteries
- Oil tray and cover to store and protect oil drums
- Magnetic locking for a greater seal and reduced contamination
- Large underbody drawer for storing old hoses
- Additional side boxes for other tool storage.
Along with the right components and storage for mobile hydraulic hose repair and replacement, the BOApod is built with a twin-axle braking system for a better grip and ensured safety in all terrains.
 (1).jpg)
2. Comprehensive training and support for hydraulic hose repair
The BOA Hydraulics team provides onsite training and ongoing support for all BOApod users. This ensures all members who are trained have the know-how to safely assemble and replace hydraulic hoses on site.
This also means that companies can get ahead of hydraulic hose failure and practice preventative maintenance and servicing on their hydraulic machinery.
This is a valuable capability when it comes to reducing unplanned downtime and minimizing oil spillage; by pre-empting hydraulic hose replacement before the hose blows, companies get the most productivity and profitability out of their machine, maximizing operational hours and achieving Hydraulic Uptime.
3. Top quality hoses and fittings
We understand the importance of a job well done, and how the right tools and products can improve performance, especially in high-pressure conditions.
That’s why BOA Hydraulics forms strong, credible partnerships that bring value to customers. As part of the BOA Integrated Solution, we source quality hydraulic products from trusted global brands, including Yokohama, Uniflex, and DNP. BOA Hydraulics is Yokohama’s preferred partner in New Zealand and Australia.
Yokohama hydraulic hoses are tested for their flexibility and durability using the rigorous Hitachi and Komatsu spike testing method. This method uses a higher-pressure cycle than normal SAE testing, at 1.2 million impulses compared with average SAE testing of 400,000-500,000 impulses.
4. BOAhub application
The fourth component of the BOA Integrated Solution, the BOAhub app, is a game-changer in hydraulic hose repair and maintenance technology.
BOAhub is a multi-device app that enables users to:
- build and save hose recipes
- manage inventory and order new stock in their mobile hydraulic hose repair facility
- plan hydraulic repair and maintenance for reduced unplanned hose failure and oil loss.
In its latest release, BOAhub now offers the Find a BOApod feature, a tool that heavy machinery operators in New Zealand can use to find their nearest local hydraulic hose repair provider.
Using geolocation tracking on each BOApod facility, Find a BOApod gives contractors an easily accessible and transparent hydraulic hose repair service experience.
As the final piece in the BOA Integrated Solution, BOAhub helps users fully manage their mobile hydraulic hose repair and maintenance activities. Having access to the right tools, training and technology gives contractors full autonomy and control over their hydraulic assets. This way, heavy machinery operators make significant savings and achieve greater Hydraulic Uptime.

Customer success with the BOA Integrated Solution
Contractors in various industries have used the BOA Integrated Solution to significantly reduce downtime and hydraulic hose repair costs.
At McDougall Logging, Arnold Henry uses the BOApod trailer to assemble and replace hydraulic hoses. “The BOApod trailer is right here on the job, so as soon as you blow a hose it’s 10 minutes and you are back up and running again.”
Thanks to the focus on quality, Yokohama hoses support heavy machinery operators with greater assurance and reduced hose failure. While falling a tree with a harvester, Logger Jody Knowles from JKL remarked: “The branches down low hooked on the three-quarter inch hose... As the tree went over, the hose got caught in the tree and the Yokohama hose would have stretched another metre, and it didn’t even blow the fitting. There was another hose beside it, which wasn’t Yokohama, and that one actually blew to bits. And this is happening across the board. Even the half-inch hoses on the Ensign grapples, they stretch as well.”
This reduction in hose failure and downtime has meant a significant drop in hose bills for many. Matt Winmill from Gillion Logging confirmed “my hose bill has gone back from $3000 a month, back to around $900” – a 70% reduction in monthly hydraulic hose bills.
Furthermore, we’re not just focused on monetary gains for contractors. BOA is committed to building awareness and capability among hydraulic machinery operators on safe practices for hydraulic hose repair and maintenance.
“Since purchasing our BOApod we have had nothing but remarkable service,” says Melissa Monaghan, from Entire Engineering. “The support has continued with staff training, meeting new clients with us, regular phone calls and visits to check in.”
Similarly, Dan Miers from Alpine Air says: “I have had nothing but great support and service from the BOA Team, when [the BOApod] was delivered the training was exceptional – I felt I could hit the ground running.”
Turn wasted time into profit with mobile hydraulic hose repair and maintenance
The BOA Hydraulics team is passionate about helping contractors increase the productivity and profitability of their heavy machinery.
We want to equip heavy machinery operators with the skills and products needed to take control of their hydraulic downtime and turn that time back into profit.
For more information about the BOA Integrated Solution and our mobile hydraulic hose repair facility, contact the BOA Hydraulics team online or call us on 0800 20 20 20 today.
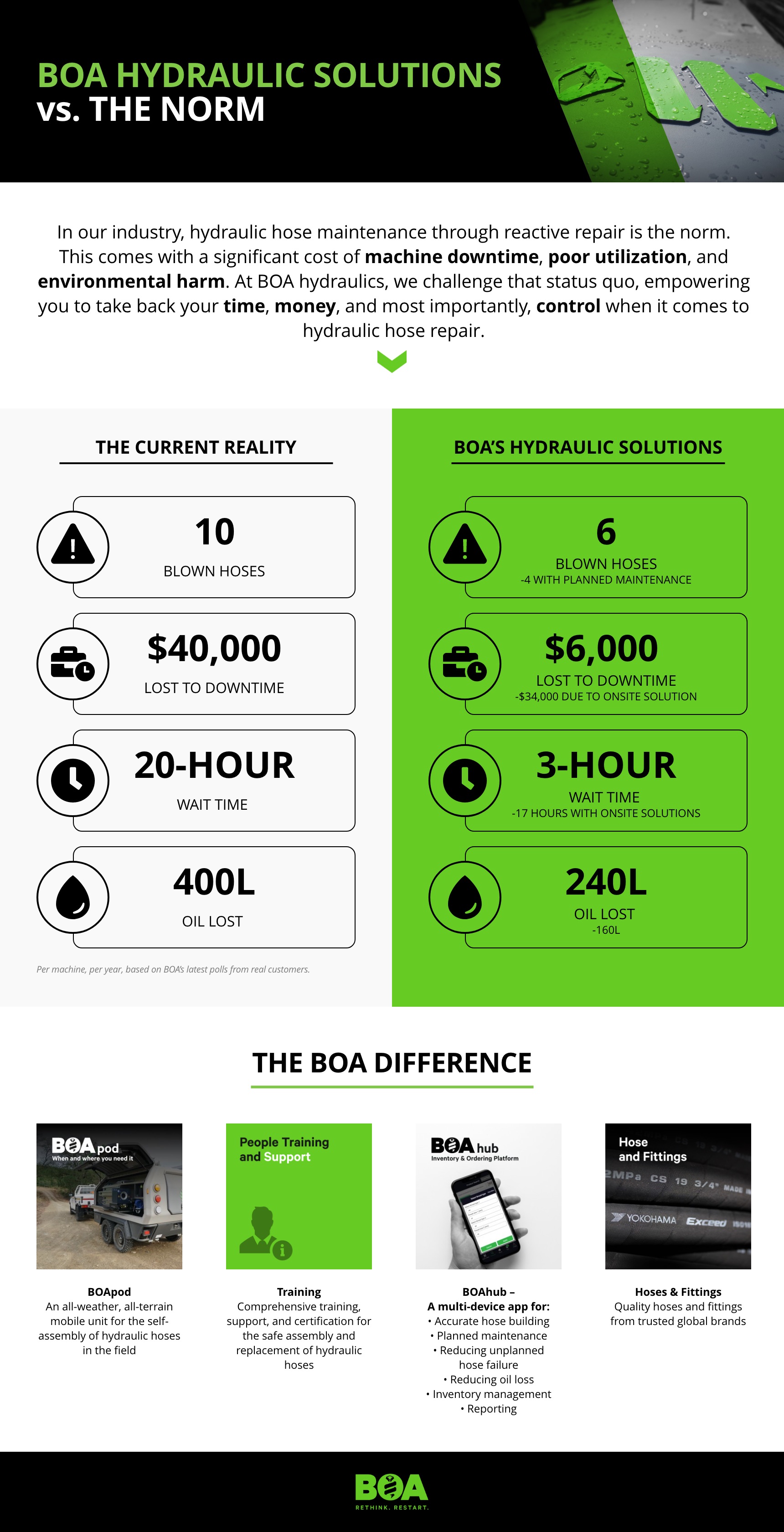